Wire You So Complicated? Unravelling the Intricacies of Wire Harness Fault Finding!
- granthutchings
- Dec 12, 2023
- 7 min read
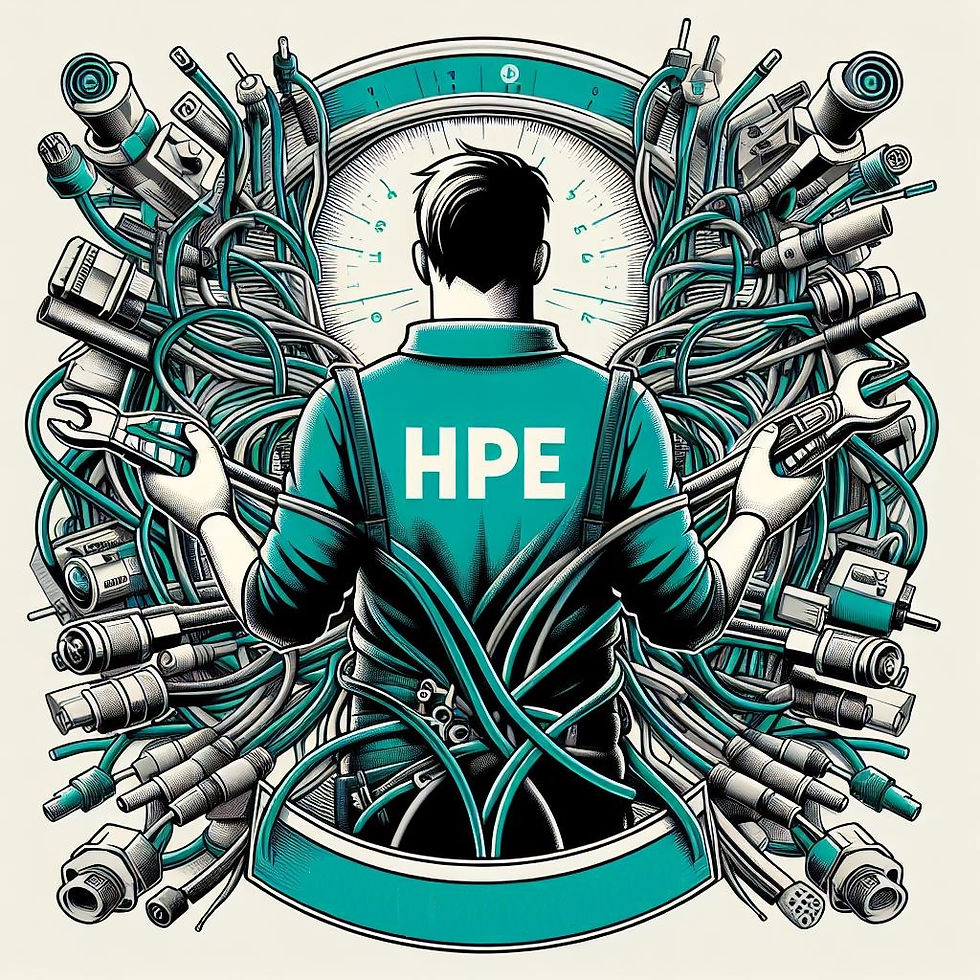
Section 1: "The Puzzle Begins: Understanding the Basics of Wire Harness Faults"
Open Circuits and Short Circuits:
Embarking on the journey of wire harness fault finding involves unravelling the complexities of both open circuits and short circuits. These faults, where wires experience interruptions or unintended contacts, demand a nuanced approach for comprehensive diagnosis.
One invaluable tool in this exploration is time-domain reflectometry (TDR). TDR operates by sending an electrical pulse down the wire and analysing reflections. When the pulse encounters an open circuit, a short circuit, or any abrupt impedance change, reflections occur. By measuring the time it takes for the pulse to travel and return, TDR can precisely calculate the distance to the fault, aiding in the identification of both open circuits and short circuits.
Open Circuits:
Understanding the intricacies of open circuits goes beyond basic continuity testing. A wire break, a physical interruption leading to a complete gap in the circuit, and a high-resistance area, which introduces resistance without severing the wire, are two key scenarios. TDR, with its high precision, allows technicians to differentiate between these scenarios. The distinct characteristics in the TDR trace aid in identifying whether the fault is a complete break or a high-resistance area, providing valuable insights into the nature of the open circuit.
High-Resistance Areas:
High-resistance areas can occur due to several factors. Corrosion, often caused by exposure to environmental elements, can introduce resistance, hindering the flow of current. Poor connections, at connectors, terminals, or splices, may result in increased resistance. Insulation damage, exposing conductors to the environment, can also lead to resistance. Additionally, overheating in areas with high electrical loads can contribute to degradation, impacting the conductive properties of wires. TDR, as a diagnostic tool, plays a crucial role in pinpointing and differentiating between these high-resistance scenarios, allowing technicians to grasp the nature of the fault accurately.
Short Circuits:
Navigating short circuits requires recognising the diverse factors that can lead to unintended contacts between wires. Unlike open circuits, short circuits can be caused by physical damage, insulation failure, crossed wires, or component failure. TDR plays a pivotal role in identifying short circuits, precisely calculating the distance to the fault and providing unique patterns in the TDR trace indicative of a short circuit.
By incorporating TDR into the fault-finding toolkit and understanding the nuances between open and short circuits, technicians gain a rapid and efficient method for locating faults with high precision. This sophisticated approach enhances the diagnostic process, ensuring a detailed understanding of wire harness faults.
Section 2: "Tools of the Trade: Essential Equipment for Precise Fault Diagnosis"
Multimeter Integration:
In the realm of wire harness fault diagnosis, the integration of the multimeter serves as a linchpin for uncovering issues. The multimeter, with its diverse measurement capabilities, aids in conducting a variety of tests. Through voltage, resistance, and continuity measurements, technicians can identify open circuits, short circuits, and high-resistance areas. The versatility of the multimeter allows for a comprehensive assessment of the wire harness, ensuring that each aspect of its electrical performance is scrutinized with precision. Whether it's checking the continuity of a wire or measuring voltage drops across components, the multimeter is a fundamental tool in the diagnostic toolkit.
Continuity Tester Advancements:
Continuity testers, with their advanced features, bring a new dimension to fault finding in wire harnesses. Traditional continuity testers alert technicians to the presence or absence of a connection, but advancements in micro-ohm measurements elevate the diagnostic process. Technicians can now identify minute changes in wire conductivity, honing in on subtle faults that may not be apparent through standard continuity testing. This precision is particularly valuable in diagnosing high-resistance areas where conventional testers might fall short. The continuity tester, enhanced with micro-ohm measurements, acts as a refined probe, allowing technicians to navigate the intricate pathways of wire harnesses with meticulous accuracy.
Specialised Diagnostic Tools:
Specialised diagnostic tools represent the pinnacle of wire harness fault diagnosis, offering advanced capabilities that streamline the process. Automated testing sequences, coupled with in-depth analysis, provide a comprehensive evaluation of the wire harness's health. These tools go beyond the basics, employing sophisticated algorithms to identify patterns, anomalies, and potential faults that might elude traditional methods. The user-friendly interface simplifies the diagnostic workflow, allowing technicians to interpret results swiftly and accurately. By embracing these specialised tools, technicians gain a holistic view of the wire harness, enabling them to navigate the complexities of fault finding with efficiency and precision. It's not just about identifying faults; it's about harnessing the power of technology to elevate the diagnostic experience.
Section 3: "Navigating the Maze: Strategies for Effective Wire Harness Repair"
Precision Splicing Techniques:
The heart of wire harness repair lies in precision splicing techniques, where the art of seamlessly joining wires takes centre stage. Technicians employ meticulous methods to address wire breaks, ensuring a robust connection that restores the circuit's continuity. This process involves careful insulation removal, precise stripping of wire ends, and the use of solder devices for secure connections. Each step contributes to creating a seamless splice, eliminating the fault and fortifying the overall integrity of the wire harness. The precision in splicing, whether through crimping or using solder devices, is critical, ensuring a reliable and long-lasting repair.
Heat Shrink Magic:
Enter the realm of heat shrink tubing, a versatile ally that adds a touch of magic to wire harness repair. Technicians use heat shrink tubing to encapsulate and protect spliced connections. Notably, solder devices come equipped with integrated heat shrink, eliminating the need for additional tubing. By applying heat, the tubing or integrated shrinkage within the solder device forms a snug and protective layer around the repaired section. This not only shields the splice from environmental elements but also enhances the overall durability of the wire harness. Available in various sizes and materials, this combined approach simplifies the repair process, ensuring that the restored section remains resilient in the face of operational challenges.
Rigorous Testing:
The culmination of the repair journey involves rigorous testing to validate the effectiveness of interventions. Technicians leverage diagnostic tools, including multimeters and continuity testers, to ensure that the repaired wire harness meets stringent performance standards. Automated testing sequences, akin to those used in fault diagnosis, come into play, validating the integrity of the repaired sections. This thorough testing phase provides technicians with the confidence that the wire harness has been successfully restored to optimal functionality.
Section 4: "Prevention is Key: Tips for Maintaining Wire Harness Health"
Protective Wrapping:
The foundation of preserving wire harness health lies in the strategic use of various protective wrapping techniques. Technicians employ a combination of convoluted tubing, loom, and heat shrink tubing with meticulous consideration. Convoluted tubing acts as a flexible and durable shield, encompassing wire bundles to safeguard them from abrasion, moisture, and environmental elements. Loom provides an additional layer of protection, offering resistance against physical damage. Heat shrink, a versatile ally in protective wrapping, provides a snug and protective layer by shrinking when heat is applied. The careful selection and application of these protective measures are crucial, tailored to the specific challenges the wire harness may encounter in its operational environment.
Secure Mounting:
Beyond the wires themselves, the longevity of a wire harness is greatly influenced by how securely it is mounted within the vehicle or machinery. Technicians meticulously employ a variety of secure mounting techniques, such as clips, clamps, cable ties, and, where applicable, heat shrink. Each securing method is chosen based on the harness's location and the potential stresses it may encounter during operation. Properly secured mounting, complemented by the use of heat shrink for added protection, mitigates movement-related wear and tear, ensuring the harness remains firmly in place. This meticulous approach contributes to the overall reliability and durability of the wire harness.
Regular Inspection:
Vigilance is the linchpin of wire harness maintenance, and regular inspections serve as the eyes and ears of proactive care. Technicians conduct thorough visual assessments, scrutinizing every inch of the wire harness for signs of wear, fraying, or exposure. This visual inspection is complemented by periodic electrical tests using diagnostic tools like multimeters. These tests delve beyond the surface, ensuring the continued integrity of the wire harness. The synergy of visual inspections and electrical tests, along with the use of protective measures like heat shrink, empowers technicians to identify potential issues before they manifest, preventing faults and preserving the performance of the harness over time.
Environmental Considerations:
Wire harness health is intricately tied to its operating environment, necessitating a nuanced approach to environmental considerations. Technicians implement protective measures tailored to the specific challenges posed by the surroundings. Heat-resistant shielding guards against extreme temperatures, shielding the harness from potential heat-induced damage. Anti-corrosive coatings act as a barrier, protecting against the corrosive impact of substances in the environment. These environmental considerations, combined with the use of protective wrapping techniques including heat shrink, form a shield around the wire harness, ensuring its conductive integrity remains intact across diverse conditions.
Summary: "Mastering Wire Harness Care and Maintenance"
Wire harnesses, the unsung heroes of electrical systems, demand careful attention to ensure longevity and optimal performance. In the realm of wire harness care and maintenance, four key pillars emerge:
Fault Diagnosis Mastery:
Technicians leverage diagnostic tools like multimeters and continuity testers for precise fault diagnosis.
Precision splicing techniques, including the use of solder devices, are applied to address wire breaks and ensure robust connections.
Heat shrink tubing, integrated within solder devices, offers a streamlined solution, eliminating the need for additional protective wrapping.
Tools of the Trade: Essential Equipment for Precise Fault Diagnosis:
Multimeters stand as versatile allies, conducting voltage, resistance, and continuity measurements for comprehensive assessments.
Continuity testers, equipped with micro-ohm measurements, bring precision to fault finding in wire harnesses.
Specialised diagnostic tools, featuring automated testing sequences and user-friendly interfaces, elevate fault identification to new heights.
Navigating the Maze: Strategies for Effective Wire Harness Repair:
Harness repair begins with a meticulous assessment of faults, identifying open circuits, short circuits, or high-resistance areas.
Precision splicing techniques, incorporating solder devices, ensure seamless wire joins and robust connections.
Heat shrink tubing, an integral part of some solder devices, adds a protective layer, streamlining the repair process.
Prevention is Key: Tips for Maintaining Wire Harness Health:
Protective wrapping techniques, including convoluted tubing, loom, and heat shrink, shield wire harnesses from abrasion and environmental elements.
Secure mounting methods, coupled with the use of heat shrink, prevent movement-related wear and tear, enhancing overall reliability.
Regular visual inspections and electrical tests, complemented by environmental considerations and protective measures, prevent faults and extend the life of the wire harness.
Mastering wire harness care and maintenance requires a holistic approach, encompassing fault diagnosis expertise, advanced tools, precise repair strategies, and proactive preventive measures. By embracing these pillars, technicians can ensure the resilience and longevity of wire harnesses in diverse operational environments.
Comments